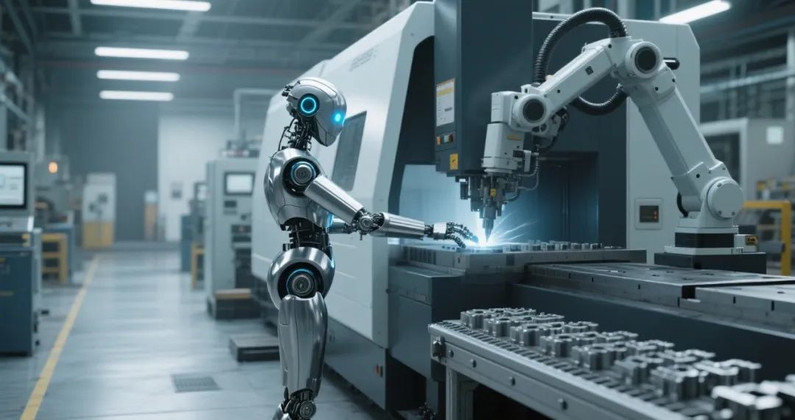
案例1:柔性生产线动态调度智能体 (汽车零部件制造)
痛点:
多品种、小批量订单激增,传统固定产线切换效率低,设备空闲率高,订单交付延迟风险大。智能体方案:
1) 部署: 在MES系统上部署调度智能体集群(每个工位/设备有代理智能体,中央有协调智能体)。
2) 感知: 实时采集订单信息(ERP)、设备状态(IoT传感器)、物料位置(RFID/AGV)、工人位置/技能(可穿戴设备)。
3) 决策: 基于实时数据和预设规则(优先级、交期、切换成本、设备能力、工人技能),中央协调智能体运用强化学习或优化算法动态计算最优生产序列和资源分配方案。
4) 执行: 智能体直接向AGV发送物料搬运指令、向设备控制器发送加工程序切换指令、向工人终端推送操作任务和指导。
5) 优化: 持续学习历史调度效果,优化决策模型(如减少切换时间权重、平衡设备负载)
效果:
设备综合效率(OEE)提升 15%+
订单平均交付周期缩短 20%
生产线切换时间减少 30%
动态响应紧急插单能力显著增强
案例2:预测性维护与自愈智能体 (高端数控机床厂商)
痛点:
关键设备突发故障导致整线停产,损失巨大;传统定期维护成本高且可能过度或不足。智能体方案:
1) 部署: 在设备边缘网关或云平台部署预测性维护智能体。
2) 感知:实时采集设备多维数据(振动、温度、电流、声发射、油液品质)。
3) 分析: 智能体运用内置的机器学习模型(如LSTM, 1D-CNN) 分析数据流,识别异常模式,预测潜在故障类型和剩余使用寿命(RUL)。
4) 决策:
- 预测到轻微异常:触发预警,建议调整运行参数(如降低负载、转速)。
- 测到中度风险:自动生成工单,安排非高峰时段维护。
- 预测到严重故障风险:立即触发安全停机指令,并通知维护人员。
- 结合备件库存智能体:自动触发备件采购申请。
5) 自愈(部分场景): 对于软件或参数类问题,智能体可自动加载备份配置或执行校准程序。
效果:
非计划停机时间减少 40%+
维护成本降低 25% (减少不必要的定期维护和紧急维修)
设备平均寿命延长 15%
案例3:端到端供应链协同智能体 (消费电子制造)
痛点:
全球供应链复杂多变(供应商延迟、物流堵塞、需求波动),牛鞭效应显著,库存高企或缺货并存。智能体方案:
1)部署:构建多智能体系统(MAS)
需求预测智能体: 分析销售数据、市场情报、社交媒体趋势 供应商协作智能体: 连接供应商系统,获取产能、交付状态、风险信息 物流监控智能体: 集成GPS、船运/空运API,实时追踪在途物料 库存优化智能体: 监控各节点库存水平(工厂、仓库、分销中心) 中央协调智能体: 全局优化决策
2)协同决策:
- 需求预测智能体发出信号 → 中央智能体综合供应商能力、在途库存、现有库存 → 运用约束优化或博弈论模型 → 生成最优采购订单、生产计划、补货策略、物流路线调整建议。
- 自动触发与供应商系统的订单确认、付款流程)。
- 动态调整安全库存水平
效果:
整体供应链库存水平降低 。
订单满足率提升至 98%+
对突发供应中断(如港口拥堵)的响应速度提升 50%
显著减少人工协调工作量
案例4:AI视觉质检智能体 (精密光学元件制造)
痛点:人工检测效率低、易疲劳、标准不一;微小缺陷(划痕、气泡、镀膜不均)漏检率高。
智能体方案:
智能体运行深度学习模型(如YOLO, Segment Anything Model) 实时分析产品图像/视频流。
精确识别、定位、分类各种预定义缺陷。
基于缺陷类型、尺寸、位置,即时判断产品合格/返工/报废。
对疑似缺陷进行多角度复检确认。
效果:
检测速度提升 10倍 (相比人工)
缺陷检出率 > 99.5% (远高于人工平均95%)
实现 100% 全检,无遗漏
测标准完全统一,数据可追溯